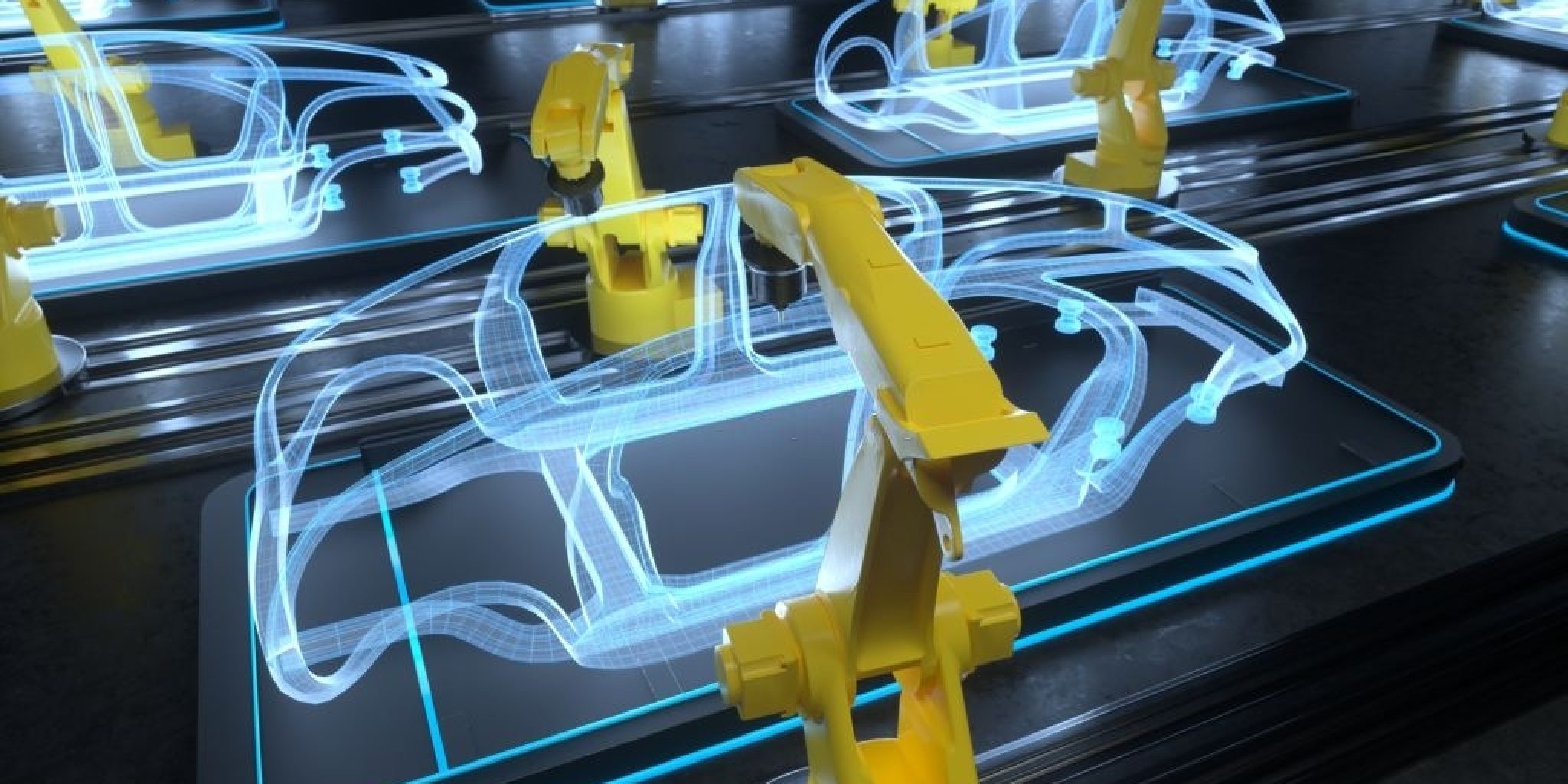
5S là phương pháp quản lý (sản xuất), công cụ quản lý theo phương pháp Nhật Bản, làm cơ sở cho các hệ thống và triết lý quản lý sản xuất như TPS, TQM và LEAN Manufacturing.
Hiện nay 5S hiện diện tại tất cả các tổ chức theo đuổi và đạt được mô hình tổ chức đẳng cấp thế giới với mục đích chính là loại bỏ các lãng phí trong sản xuất, giảm thiểu các hoạt động không gia tăng giá trị, cung cấp một môi trường làm việc với tinh thần cải tiến liên tục, cải thiện tình trạng an toàn và chất lượng.
Tại sao nên thực hiện 5S?
Từ văn phòng, nhà kho cho đến công trường xây dựng, hay nhà xưởng công nghiệp hoặc nông nghiệp. Nơi nào có hoạt động thì nơi đó cần sắp xếp, cần phân loại, cần sạch sẽ, các thiết bị sản xuất hoạt động trong môi trường phù hợp với tiêu chuẩn chất lượng an toàn.
Thực hành 5S là một chương trình đòi hỏi sự tham gia của tất cả mọi người trong tổ chức/doanh nghiệp. Đây là một phương pháp hiệu quả để huy động con người, cải tiến môi trường làm việc và nâng cao năng suất. Nguyên tắc của thực hành 5S hết sức đơn giản, không đòi hỏi phải dùng các thuật ngữ hay phương pháp phức tạp nào trong quá trình thực hiện. Thành công trong thực hành sẽ giúp các tổ chức/doanh nghiệp đạt được năng suất cao hơn thông qua:
- Xây dựng một môi trường sạch sẽ, ngăn nắp. 5S ngăn chặn sự xuống cấp của nhà xưởng, tạo sự thông thoáng cho nơi làm việc, đỡ mất thời gian cho việc tìm kiếm vật tư, hồ sơ cũng như tránh sự nhầm lẫn.
- Mọi người trong cũng như ngoài tổ chức/doanh nghiệp dễ dàng nhận thấy rõ kết quả.
- Tăng cường phát huy sáng kiến cải tiến các hoạt động sản xuất kinh doanh.
- Nâng cao ý thức kỷ luật trong cơ quan.
- Chỗ làm việc trở nên thuận tiện và an toàn.
- Giúp cán bộ công nhân viên làm việc cảm thấy thoải mái, làm việc có năng suất cao và tránh được sai sót.
- Xây dựng hình ảnh tổ chức/doanh nghiệp, đem lại cơ hội trong quản lý, kinh doanh…
Theo từ gốc tiếng Nhật, 5 chữ S trong mô hình 5S là viết tắt của Seiri (Sàng lọc), Seiton (Sắp xếp), Seiso (Sạch sẽ), Seiketsu (Săn sóc), Shitsuke (Sẵn sàng).
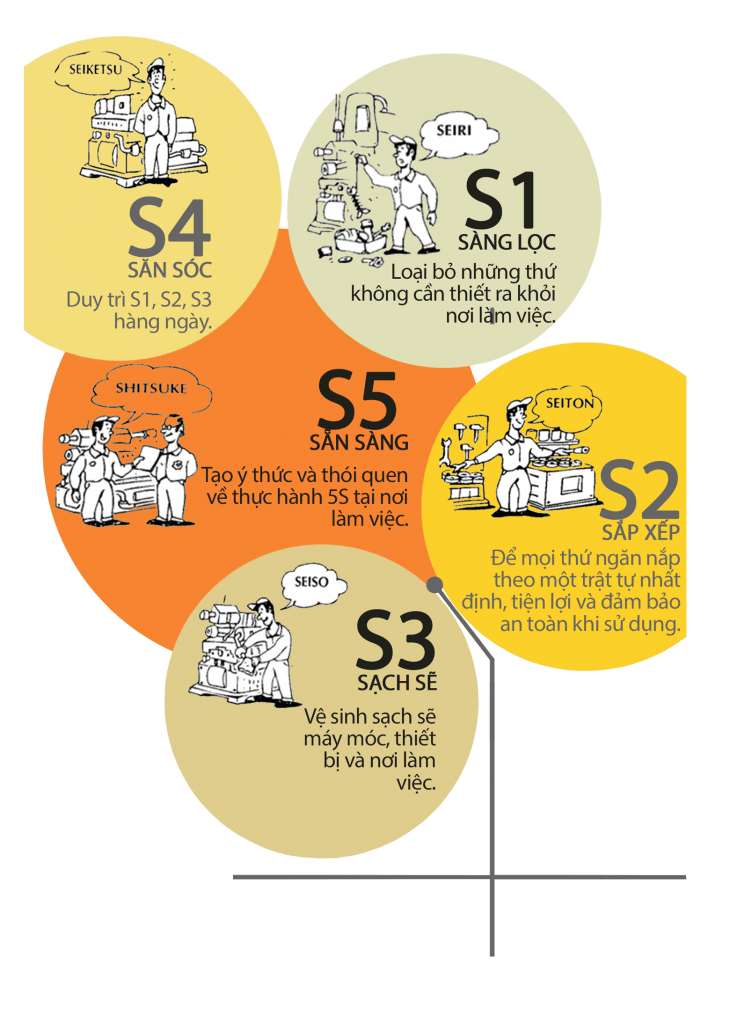
Bước 1 (Seiri – Sàng lọc) – Tổng vệ sinh, sàng lọc và phân loại

Trong bước này, điều quan trọng nhất là mọi người trong tổ chức cần đảm bảo xác định và phân loại được các dụng cụ, đồ dùng theo tần suất sử dụng:
- Những thứ chắc được cần đến thường xuyên trong quá trình sản xuất.
- Những thứ thình thoảng cần đến trong quá trình sản xuất.
- Những thứ được cho là không còn được cần đến trong tương lai.
- Những thứ mà tổ chức không cần đến nữa.
Trong quá trình này, cần đảm bảo tổ chức BIẾT một cách chắc chắn về những câu trả lời này chứ không chỉ dừng lại ở những suy nghĩ và suy luận, và mọi người luôn nhớ rằng các vận dụng thừa ra không dùng đến cũng gây ra lãng phí về mặt tiền bạc để cất giữ. Vì vậy, nguyên tắc đơn giản là “Đừng giữ những gì mà tổ chức không cần đến”!
Khi thực hiện sàng lọc, cần đảm bảo việc loại bỏ những lãng phí ngay tại nguồn thông qua 7 bước sau đây:
- Xác định mức độ bụi bẩn / rò rỉ.
- Thực hiện việc tổng vệ sinh.
- Tìm hiểu nguyên nhân gốc rễ của các hiện tượng phát hiện trên hiện trường.
- Xác định những khu vực “xấu” nhất trong nhà máy / phạm vi xem xét.
- Liệt kê một cách chi tiết các nguyên nhân cho khu vực này.
- Quyết định phương châm hành động hiệu quả.
- Lên kế hoạch tiến độ và ngân sách (nếu cần thiết) cho việc triển khai.
Bước 2 (Seiton – Sắp xếp) – Sắp xếp bố trí lại các khu vựcc và phân loại
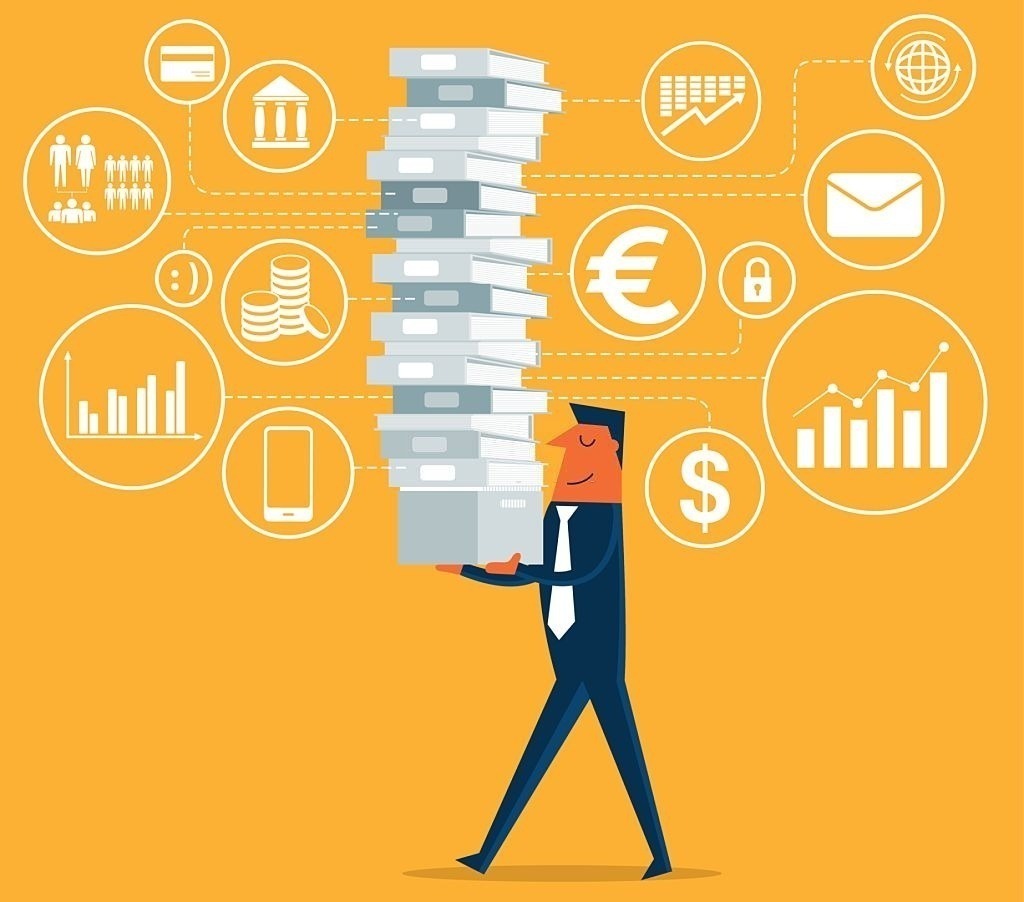
Trong giai đoạn này mọi thứ cần được xếp đặt vào đúng chỗ của mình, và để như vậy, cần tổ chức khu vực lưu giữ cho các thiết bị/dụng cụ thông qua việc trả lời các câu hỏi như: “Cái gì?” “Ở đâu?”, “Bao nhiêu?”, …
Nguyên tắc bố trí các vị trí lưu giữ là dựa trên tần xuất sử dụng: những thứ thường xuyên sử dụng được sắp xếp gần với vị trí làm việc, những thứ ít sử dụng được sắp xếp xa vị trí làm việc. Trong phạm vi khu vực sản xuất, tổ chức cần xác định rõ ràng các khu vực đi lại, khu vực làm việc, khu vực nghỉ ngơi, … . Các màu sắc khách nhau có thể được sử dụng để phân biệt mỗi khu vực (ví dụ: màu đỏ cho các vị trí để trang thiết bị phòng cháy chữa cháy, và các khu vực nguy cơ cao về an toàn, màu vàng cho giới hạn khu vực đi lại). Cần lưu ý để các vật dụng thiết yếu như bình chữa cháy và các trang thiết bị an toàn luôn dễ nhìn và dễ tiếp cận.
Các vị trí lưu giữ cần được đảm bảo thích hợp với mục đích sử dụng, được duy trì tốt, các dụng cụ dễ được tìm thấy, có hình thức nhận biết rõ ràng với dụng cụ và các vị trí. Điều quan trọng là có vị trí cho từng thứ và mọi thứ phải ở đúng vị trí.
Bước 3 (Seiso – Sạch sẽ) – Thường xuyên vệ sinh và kiểm tra
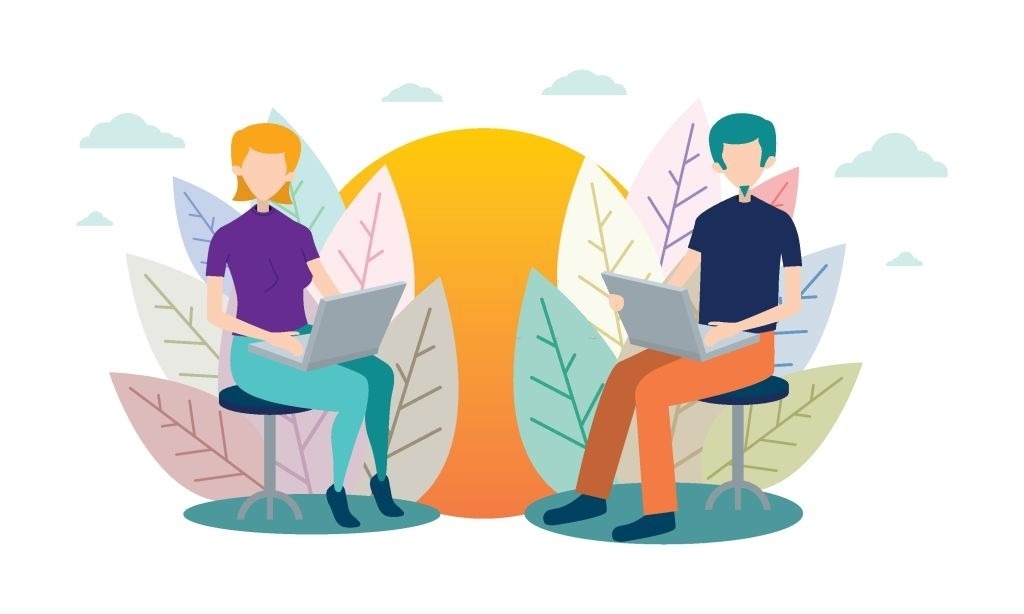
Tổ chức cần lên kế hoạch cho việc kiểm vệ sinh thường xuyên để tạo ra và duy trì một môi trường làm việc gọn gàng và sạch sẽ. Trách nhiệm cần được thiết lập và gắn cho từng khu vực cụ thể và đảm bảo quy định rõ ràng về vai trò và trách nhiệm trong việc về sinh và kiểm tra. Trong bước này, tổ chức cần thiết lập được các chu trình thường xuyên cho duy trì môi trường làm việc sạch sẽ (ví dụ: 5 phút 5S mỗi đầu cuối ngày, 30 phút 5S mỗi chiều Thứ Sáu). Một điều cần quan tâm là đảm bảo việc vệ sinh phải trở thành một hoạt động thường xuyên, liên tục, được giám sát, mọi nhân viên coi đó là niềm tự hào và giá trị đóng góp cho tổ chức.
Sự sạch sẽ là một điều kiện cơ bản cho chất lượng, vì vậy, một khi khu vực làm việc đã sạch sẽ, nó cần được duy trì.
Bước 4 (Seiketsu – Săn sóc) – Duy trì tiêu chuẩn về sự sạch sẽ, ngăn nắp
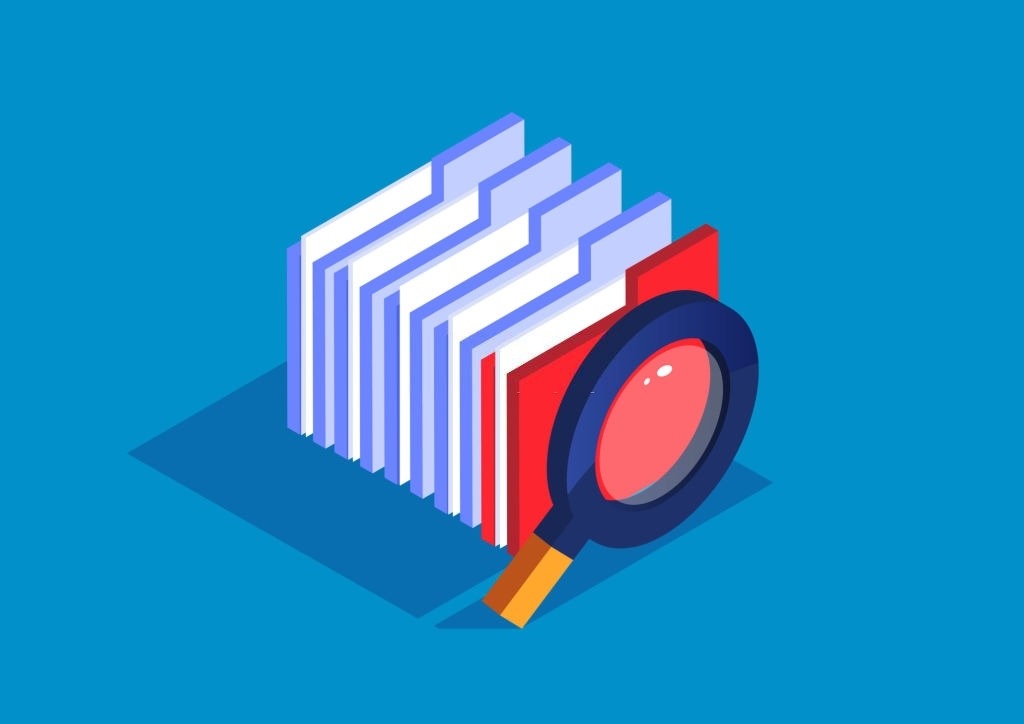
Tổ chức cần xác định tiêu chuẩn cho những điều được coi là bất thường và làm cho chúng trở nên trực quan, dễ nhận biết đối với nhân viên. Điều này bao gồm:
Việc thiết kế các nhãn mác rõ ràng và tiêu chuẩn cho các vị trí, dụng cụ, thiết bị và đặt chúng ở những vị trí quy định.
Hình thành các chỉ số (và cách nhận biết) khi các giới hạn bị vượt (ví dụ đồng hồ áp lực, đồng hồ nhiệt độ, mức nguyên liệu trong thùng nạp,…)
- Vẽ sơ đồ đánh dấu vị trí khi các đồ vật/dụng cụ được mang đi hoặc trả lại vị trí.
- Ngoài ra, duy trì tiêu chuẩn cũng cần đến việc thiết lập, thống nhất và duy trì:
- Tiêu chuẩn về sự sạch sẽ.
- Các quy trình để duy trì tình trạng tiêu chuẩn.
- Đánh dấu và ghi nhãn thống nhất cho toàn bộ các đồ vật/dụng cụ.
- Thiết lập phương pháp thống nhất cho chỉ thị về giới hạn, xác định các vị trí,….
Bước 5 (Shitsuke – Sẵn sàng) – Hình thành thói quen và thực hành
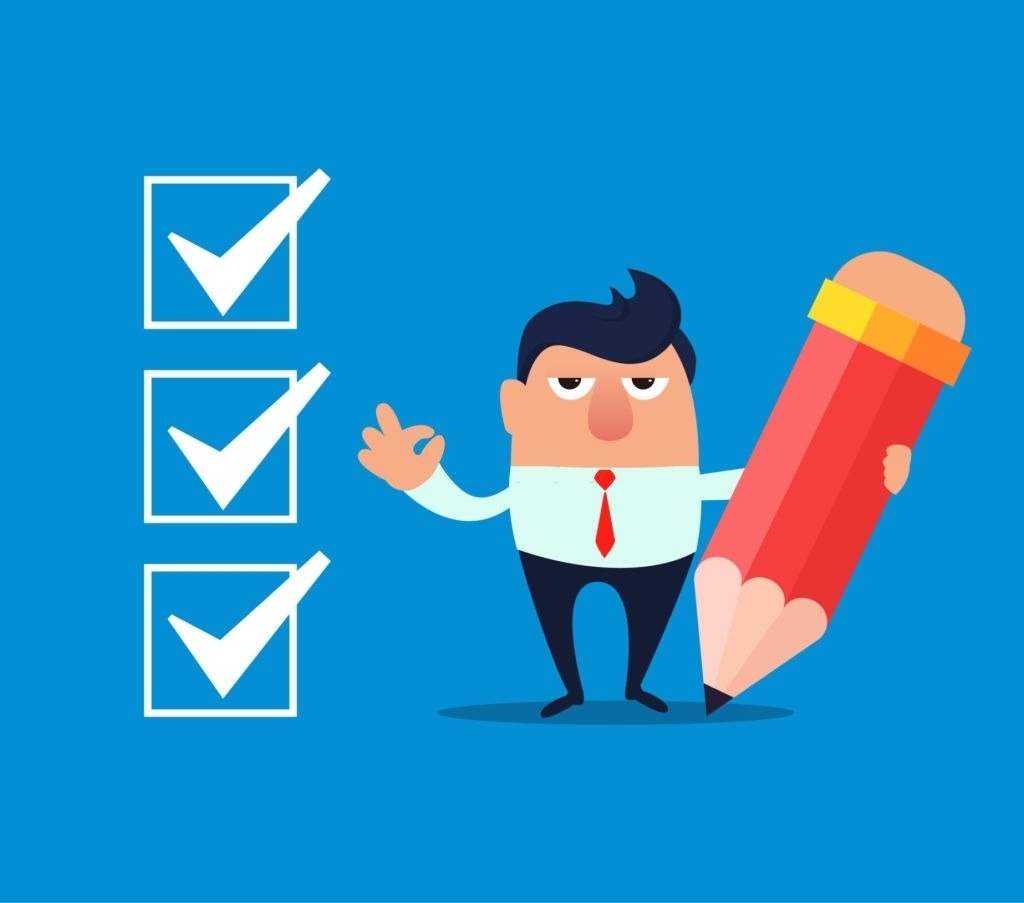
Cũng như đối với việc áp dụng công cụ nâng cao năng suất chất lượng nào, khó khăn lớn trong thực hiện 5S là việc tuân thủ các quy định, việc áp dụng thực hành 5S đòi hỏi sự cam kết và ủng hộ của Lãnh đạo cao nhất thông qua việc chỉ đạo thực hiện, tập trung nguồn lực, kinh phí và thời gian. Vì vậy, tổ chức cần hình thành và củng cố các thói quen thông qua hoạt động đào tạo và hướng dẫn mọi cán bộ nhân viên trong tổ chức/doanh nghiệp hiểu rõ mục tiêu, ý nghĩa cũng như phương pháp để thực hiện. Từ đó mỗi phòng ban/phân xưởng có thể chủ động đưa ra kế hoạch thực hiện tại đơn vị của mình. Bên cạnh đó, tổ chức cần xây dựng các chính sách thưởng phạt phù hợp để khuyến khích cán bộ công nhân viên tích cực thực hiện nội quy
Trong bước này, việc đào tạo các quy trình mới nên được thực hiện thông qua các hình ảnh trực quan hơn là lới nói, và luôn đảm bảo mọi người (liên quan) đều tham gia vào việc phát triển các tài liệu tiêu chuẩn như bảng kiểm tra, tiêu chuẩn thao tác. Ngoài ra, tổ chức cần đảm bảo các thực hành đúng được đào tạo và trình diễn, trong khi các thực hành không đúng phải được nhận biết và xử lý. Hãy đảm sự tham gia của tất cả mọi người – Bí quyết thành công của chương trình thực hành 5S là tạo một môi trường khuyến khích mọi người tích cực tham gia, phát huy sáng kiến và duy trì, cải tiến không ngừng, tạo nên một nguyên tắc hoạt động trong tổ chức/doanh nghiệp để đảm bảo tính hiệu quả trong quản lý và kinh doanh. Đây cũng là yếu tố quan trọng nhất để thực hiện thành công chương trình thực hành 5S.
Nguồn tham khảo: eduviet, wikipedia.
Bình luận