Maintenance consists of actions that are taken buy replica watches to prevent a device or a component of a system from failing. This also includes repair of normal equipment degradation to keep the operation of the device in proper working 1:1 replica watches order. Ideally, maintenance is performed to keep equipment and systems running efficiently at least during its design life.
Maintenance activities are omega Replica Watches structured as follows:
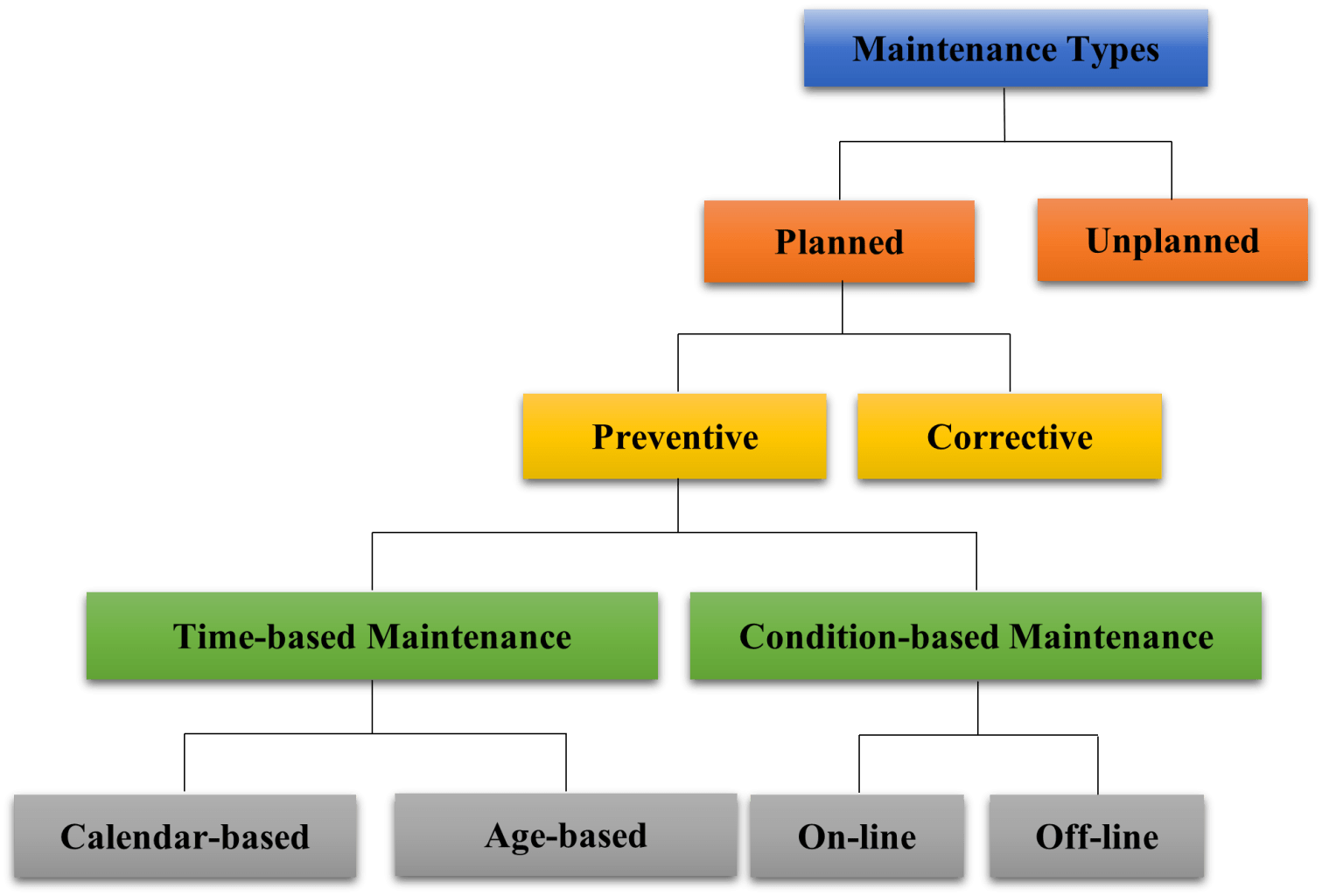
1. Planned Maintenance
Preventive maintenance: This can be defined as to perform actions on a “time- or machine-run-based schedule”. This schedule is aimed to detect, preclude, or mitigate degradation of a component or system to sustain or extend its life by controlling degradation to an acceptable level. All the actions are performed on a periodic way whether the system reaches its design life.
- Time-based maintenance (TBM): This can be defined as the measurements which are based on a predetermined maintenance plan/schedule. The maintenance actions are repeated every year/month/week/day.
Advantages | Disadvantages |
– Cost effective in many capital-intensive processes. – Flexibility allows for the adjustment of maintenance periodicity. – Increased component life cycle. – Energy savings. – Reduced equipment or process failure. | – Catastrophic failures still likely to occur. – Labor intensive. – Includes performance of unneeded maintenance. – Potential for incidental damage to components in conducting unneeded maintenance. |
-
- Calendar-based maintenance: This is the most traditional way to carry out maintenance activities, based on a calendar schedule. Maintenance activities are planned in advance mostly according to recommendations of manufacturers or operators’ experiences.
- Age-based maintenance: This is another kind of scheduled maintenance performed when the operational time of an equipment reaches the planned cumulative operating time.
- Condition-based maintenance [CBM]:
- Online (Real-time or Near real-time maintenance): This can be defined as measurements which receive real-time or near real-time meter readings to create work orders.
Advantages | Disadvantages |
– Increase highly and accurately system reliability. – Ensure system availability as it provides early detection of deterioration and therefore enough time for appropriate planning. – Reduce spare parts inventory as it predetermines the exact number of the required spare parts. – Increase safety as it bases on meter readings of high pressure, high temperature, flammable fluids, etc. – Reduce maintenance costs as it reduces redundant maintenance actions. – Highly reduce downtime. | – Traditional organization is based on predetermined maintenance tasks. Any change may make difficulties. – Need to have accurate data (and data management) from SCADA. – Planning of maintenance actions is slow as it moves from static intervals of periodic maintenance to a dynamic one of CBM. |
-
- Offline (Predictive maintenance): This can be defined as measurements that detect the “onset of system degradation”. This is to allow causal stressors to be eliminated or controlled prior to any significant deterioration in the physical state. Actions are performed at the time of lower functional state.
Advantages | Disadvantages |
– Increased component operational life/availability. – Allows for preemptive corrective actions. – Decrease in equipment or process downtime. – Decrease in costs for parts and labor. – Better product quality. – Improved worker and environmental safety. – Improved worker morale. – Energy savings. | – Increased investment in diagnostic equipment. – Increased investment in staff training. – Potential risks for critical equipment if diagnostic results are not accurate. |
- Corrective maintenance: This can be defined as the maintenance performed right after an equipment failure. This is also referred to as “failure-based maintenance” because the equipment is operated until it fails. This kind of maintenance is most cost-effective for non-economical type of equipment or non-repairable parts. Operators just replaces broken-down items.
2. Unplanned Maintenance
This is the most unexpected maintenance operators want to do. It is related to unplanned occurrences which requires urgent actions. If operators do not prepare enough resources for such a type of maintenance, downtime can be prolonged.
It is not just limited to any single maintenance type when building a maintenance program. It is best to combine these maintenance types to take the advantages of each type in a program. With more than 20 years of successful implementation of asset management and equipment maintenance projects in Vietnam, TrueTech usually analyzes the current management and maintenance data to build the most appropriate maintenance program with enterprises.
Comments