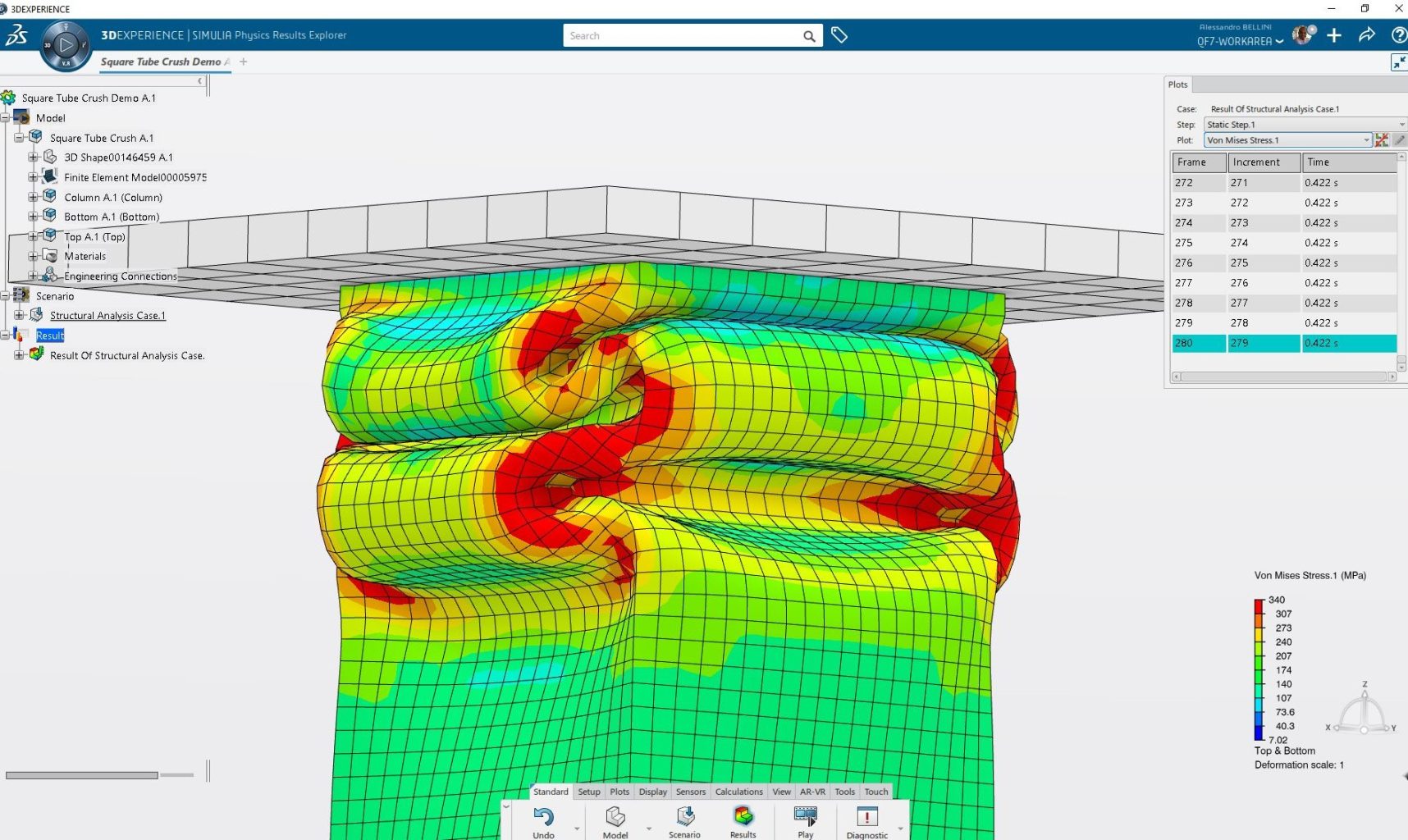
Resources
True Technology Co., Ltd proudly presents Abaqus, a powerful and comprehensive finite element analysis (FEA) software suite that empowers engineers to simulate the real-world performance of products and materials under realistic operating conditions. With advanced multiphysics simulation capabilities, Abaqus is the ideal solution for industries demanding high accuracy and efficiency.
Industry Challenges
In today’s competitive landscape, manufacturers face numerous challenges, including globalization, cost reduction, and shorter development cycles.
Reducing reliance on costly physical testing.
Optimizing designs and reducing product weight.
Evaluating the effectiveness of alternative materials.
Ensuring optimal product performance.
Abaqus Unified FEA Solution
Abaqus offers a scalable suite of unified analysis products that enable users of all skill levels to collaborate and seamlessly share simulation data.
Abaqus/Standard
Ideal for static, low-speed dynamic, and nonlinear analyses.
Abaqus/Explicit
Specialized for high-speed dynamic and impact events.
Abaqus Multiphysics
Simulates the interaction of multiple physical phenomena, such as mechanics, thermal, electromagnetic, and fluid flow.
Abaqus/CAE
A powerful and intuitive modeling, pre-processing, and post-processing environment.
Key Benefits
FEA and Multiphysics
Simulate linear and nonlinear behavior, complex materials, contact, fracture, and failure.
High-Performance Computing (HPC)
Powerful scalability for large-scale simulations..
CAD Integration
Direct connectivity with leading CAD systems like CATIA, SolidWorks, and Pro/ENGINEER.
Process Automation
Streamlined workflows and reduced analysis time.
Extensive Material Library
Supports a wide range of materials, from metals to composites.
Key Functions
Simulate various design attributes is required to perform product simulation
Collaborate and seamlessly share simulation data and approved methods without loss of information fidelity
Modeling, visualization, and best-in-class implicit and explicit dynamics FEA
Offers a comprehensive meshing environment and provides a variety of sophisticated approaches for simplifying and speeding up mesh creation
Leverage the complete range of solver analysis functionality, such as contacts, loads, boundary conditions, connectors, damage, fracture, and failure
Geometry: point, line, surface, solid. Tool for editing geometry (ex : Extrude, rotate, cut, mirror)
Mesh 1D – 2D – 3D: Auto Mesh and control of size mesh by user. Adaptive Remeshing
Element Library: beams, membrane, shells, solids, user elements
Linear/Non linear static and dynamic analysis using AMS eigen solver for large models
Implicit solver for structural buckling, post- buckling and collapse analysis
Coupled fluid-structural interaction to model wave-structure interaction
Coupled implicit and explicit to assess remaining strength after impact/blast analysis
Fully coupled Eulerian- Lagrangian (CEL) for spud can analysis
Underwater shock analysis for both deep and shallow water
Transferring material damage cross implicit and explicit analysis